HVAC Pressure Switches: Technical Principles, Types, and System Integration
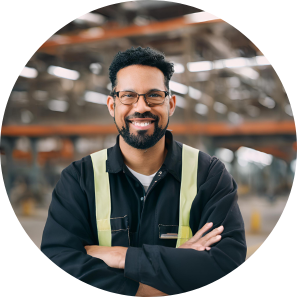
Opinion | Apr. 21st, 2025
Michael James Anderson
Pressure Product Line Manager
In HVAC systems, an air-conditioning pressure switch is an essential safety device and control component that monitors the refrigerant pressure within the system.
It functions by actuating electrical contacts at predefined pressure setpoints, thereby safeguarding equipment and optimizing operational efficiency. This article provides a comprehensive overview of the definition, operating principles, classification, applications, selection criteria, installation procedures, maintenance practices, and technological innovations pertaining to pressure switches used in HVAC applications.
Definition and Purpose
An air-conditioning pressure switch is a mechanical-electrical device that employs a pressure sensing element—such as a diaphragm, bellows, Bourdon tube, or piston—to detect refrigerant pressure. It acts as a protective relay by interrupting or closing the control circuit when the pressure crosses preset thresholds, thereby preventing compressor damage, system overpressure, or underpressure conditions. Its primary functions include system protection, cycle control, and energy efficiency optimization.
Operating Principles
Types of Pressure Switches in HVAC Systems
Applications
Selection Criteria
Installation and Maintenance
Anwoll pressure switch
Anwoll is a leading developer of pressure measurement and applications, with a mature series of pressure switches suitable for daily and cutting-edge applications.
If you would like to learn more about our pressure switches, please contact us directly.